Heat Exchanger & Condenser Tube Rolling/Retubing Training 20th – 24th January 2025 (Weekdays)
- Description
- Reviews
Course Description
Heat exchangers are crucial in various industrial processes, and maintaining their efficiency is essential for smooth operations. One of the critical maintenance tasks is retubing, which involves removing and replacing the tubes.
This Tube Rolling/Retuning Training is designed to cover the entire retubing process from preparation to execution and post-maintenance checks. The training course will also familiarize engineers and technicians with the various standards and practices used for design, manufacture, operation and maintenance of heat exchangers.
To all these engineers with diverse backgrounds and expertise, the principle of heat exchangers design and codes will allow them to understand the recommended practices. This training course will cover all these aspects with respect to engineering design in general and shell and tube exchangers in particular.
Course Objectives
- Understand heat transfer fundamentals
- Analyse the exchanger operational parameters
- Determine correct troubleshooting techniques
- Determine the correct selection criteria for heat exchangers
- Troubleshooting heat exchanger problems
Who Should Attend?
- Maintenance Professionals
- Inspection Personnel
- Process Supervisors
- Plant Operators and Technicians
- Plant and maintenance Engineers
Course Details/Schedule
Day 1
- Types and Applications of Heat Exchangers
- Overview and Basic Fundamentals
- Shell and tube
- Plate and frame
- Air-cooled
- Heat transfer principles and the role of tube bundles.
- Common issues in heat exchangers requiring retubing (corrosion, erosion, fouling, mechanical damage).
- Materials of Construction & Fabrication
- Key components of shell-and-tube heat exchangers:
- Tube sheets, baffles, tie rods, and spacers.
- Tubing materials: copper, stainless steel, titanium, and alloys.
- Tube arrangements: straight tubes, U-tubes, and their specific applications.
- Design considerations for retubing: pressure, temperature, and flow characteristics.
- Heat Transfer Fundamentals and Heat Transfer Coefficients
- Geometry of Shell & Tube Heat Exchangers (STHE)
- Double Pipes TEMA Nomenclature, Front End Head Types, Shell Types
- Rear End Types, Double Pipe Units, Selection Guidelines
- Thermal and Hydraulic Design of Heat Exchangers
- Sizing and Specifying the Heat Exchanger
- Flow vs. Temperature Difference in STHE
- Temperature Difference in STHE
- Condensers and Reboilers
- Design of Heat Exchangers
- Materials of Construction of Heat Exchangers
- Operation of Heat Exchangers
- Fouling in Heat Exchangers
- Corrosion and Erosion in Heat Exchangers
- Heat Exchanger Inspection Methods
- Operation and Troubleshooting
- Performance Monitoring and Testing
- Heat Transfer Improvement Techniques
- Finned Tubes
- Heat Integration Basics
- Pinch Technology
- Heat Exchanger Train Optimization
Day 2
- Common causes of tube degradation:
- Corrosion: uniform corrosion, pitting, galvanic corrosion.
- Erosion: due to high-velocity fluid flow.
- Stress Corrosion Cracking: from cyclic stresses and corrosive environments.
- Mechanical wear: from tube vibration or improper installation.
- Identifying early signs of tube failure using non-destructive testing (NDT).
- Vibration Considerations
- Causes of vibration
- Possible types of damage
- Design and operating parameters affecting vibration
- Potential solutions to vibration problems
- Maintenance and Repair
- Evaluating the suitability of corroded components
- Typical maintenance and inspection procedures
- Locating leaks
- Leak repairs
- Retubing considerations and preparations
- Initial inspection and diagnosis:
- Ultrasonic testing, eddy current testing, and visual inspection techniques.
- Tube removal planning:
- Identifying the scope of retubing: partial or full replacement.
- Safety considerations: safe handling of tubes and high-temperature materials, use of personal protective equipment (PPE).
- Typical cleaning methods
- Tube inspection techniques
- Rerating exchangers
- Heat Exchanger Tube Side Maintenance
- Repair vs. Replace ‐ Factors to Consider
- Heat Exchanger maintenance Options
- Heat exchanger Bundel (Hydraulic/mechanics/lifting plan)
- Repair option
- Plug
- Sleeving
- Tube Expansion
- Tube Removal Process
- Step-by-step guide to tube removal:
- Draining and decontamination of the heat exchanger.
- Methods of tube removal: mechanical extraction vs. hydraulic pulling.
- Precautions to prevent damage to tube sheets and shell.
- Removal of tube stubs and debris.
- Tube Installation Process
- Tube Preparation:
- Tube material selection and cutting to required lengths.
- Cleaning and deburring of tubes.
- Expansion requirements based on tube materials.
- Tube Installation:
- Tube positioning and insertion into tube sheets.
- Tube-to-tube sheet expansion methods:
- Mechanical rolling
- Hydraulic expansion
- Ensuring proper alignment and fit of new tubes.
- Replacement option
- Re-bundling
- Complete replacement
- Retubing
- Chiller Retubing
- Condenser Retubing
- Absorbers Retubing
- Lube Oil cooler retubing
- Boiler Retubing
- Heat Exchanger Retubing
- U-tube bundle retubing-replacement
Day 3
- Troubleshooting and Heat exchangers’ problems
- Tube Bundle Replacement ‐ Alternative Enhanced Tube Bundle Designs
- Tube bundle extraction and transporting
- The Aerial Bundle Extractor / Hydraulic Tube Bundle Extractor
- Heat Exchangers maintenance procedure phases:
- tube bundle extraction: with aerial bundle extractor /with truck mounted
- tube bundle transport
- bundle cleaning
- Tube bundle Insertion
- Heat exchanger retubing by tube sheet cutting method/without tube sheet cutting method
- Documents required for retubing
- Method statement (Repair procedure)
- Inspection Test plan (ITP)
- Tube-to-Tube Sheet Joint Integrity Testing
- Leak testing methods:
- Hydrostatic testing: pressurizing the shell side or tube side.
- Pneumatic testing: air pressure leak testing.
- Non-destructive testing (NDT) for joint integrity:
- Dye penetrant, radiographic, and ultrasonic testing.
- Welding Procedure Specification (WPS) &Procedure Qualification Record (PQR)
- Welding and Brazing Techniques
- When and how welding or brazing is required for tube joints.
- Welding procedures:
- Preparation, joint configuration, and post-weld inspection.
- Brazing procedures for specific materials (e.g., copper tubes).
- Welder Qualification Test Record (WQTR)
- Tube Expansion Procedure (TEP)
- NDT Procedures
- Hydro Test Procedures & Pneumatic Test Procedures
- A Case Study on Procedure Standardization of Heat Exchanger Retubing in Oil and Gas Industries
- Cost‐ Effective Maintenance and Repair of Heat Exchangers
- Tube Cleaning Projectiles
- Metal tube cleaners
- Water blasting with high pressure
- Chemical cleaning
- Mechanical cleaning with water propulsion and metal tube cleaners
- Benefits of cleaning with metal tube cleaners
- Safety Considerations
- Quality of cleaning
- Misconceptions about metal tube cleaners
Day 4
- Abrasive projectiles
- Tube projectiles
- Grinding projectiles
- Ultra clean projectiles bulk
- Tube projectiles bulk
- Product recovery projectiles
- Tube Cutting and Preparation
- Pipe Reamers
- Pipe Cutters
- Power Pipe Cutting
- Copper / Stainless Cut & Prep
- Tubing Cutters
- Plastic and Multilayer Cutters
- Reamers, Deburring Tools
- Pipe Cutter Selection
- Heavy‐ Duty Pipe Cutters
- Wheel Pipe Cutters
- Wide‐ Roll Pipe Cutter
- Hinged Pipe Cutters
- Power Pipe Cutters
- Copper & Stainless-Steel Cutting Prep Machine
- Midget Cutters for Close Quarters Tubing
- Plastic & Multilayer Pipe Cutters
- Tube Stubs Removal
- Traditional Stub Removal
- Induction Heat Stub Extraction
- Induction Heating Tube Shrinking
- Cooling
- Extraction
- Induction Heat‐ and‐ Pull
- Advantages of pulling stubs
- Troubleshooting Retubing Issues
- Common retubing issues:
- Leaking tube-to-tube sheet joints.
- Misalignment of tubes.
- Tube sheet deformation.
- Techniques for addressing these issues during or after retubing.
- Hands-on Retubing Practice
- Practical exercises for tube removal, cutting, cleaning, and expansion.
- Installation and testing of new tubes in a mock heat exchanger setup.
- Hands-on experience with tube pulling, rolling, and testing tools.
Day 5
- Tube facing equipment
- Facing pressure
- Securing the pipe
- Adjust, align and secure
- Cleaning
- Pipe ends extending through the jaw clamps to permit complete facing
- Finishing the facing the of the pipe
- Tube Leaks Elimination
- Solving heat exchanger problems
- Excessive load
- Gradual fouling buildup, harming heat transfer
- Excessive stream pressure loss
- Failing heat exchanger equipment
- Inadequate heat transfer
- Inadequate pressure or temperature rating
- Instrumentation
- Detection of leaks in a liquid‐ liquid heat exchanger using passive acoustic noise
- Maintenance Best Practices
- Routine inspection and cleaning methods to extend the lifespan of tubes.
- Fouling prevention: chemical treatments, mechanical cleaning.
- Tube vibration prevention using proper baffle design and tie rods.
- Post-Installation Quality Checks
- Final inspection after retubing:
- Ensuring proper tube expansion and joint integrity.
- Conducting visual and non-destructive inspections.
- Documenting retubing work for future maintenance.
- Case Studies and Industry Applications
· Review of real-world retubing projects in industries like power generation, oil and gas, and petrochemicals.
· Lessons learned and best practices from past retubing operations.
- Safety and Environmental Considerations
· Environmental guidelines for handling old tubes (e.g., dealing with hazardous materials like asbestos or lead-based coatings).
· Safety protocols during retubing in confined spaces or in high-temperature environments.
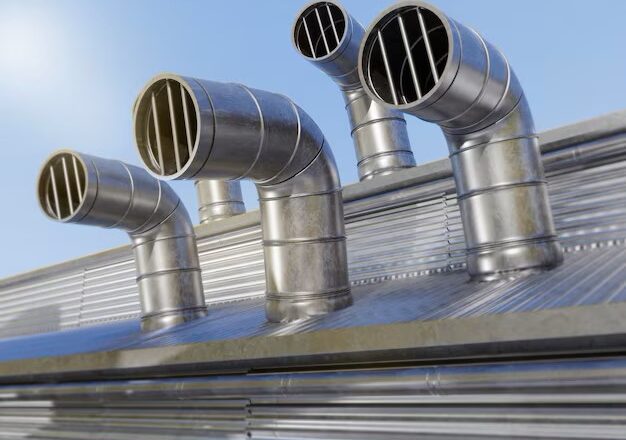