Overview of Refinery Process: The Catalytic Reforming Process 2nd – 6th June, 2025
- Description
- Reviews
Course Overview
This 5-day course provides an in-depth overview of the catalytic reforming process in petroleum refineries. It covers the principles of catalytic reforming, its operational aspects, and how it contributes to the production of high-octane gasoline components. Participants will explore the catalyst types, reactor design, process conditions, and troubleshooting strategies essential for optimising catalytic reforming operations. The course is ideal for refinery engineers, operations managers, and technical professionals involved in refining and gasoline production.
Course Objectives
By the end of this course, participants will be able to:
- Understand the principles and chemistry behind catalytic reforming.
- Identify the key components and equipment involved in catalytic reforming.
- Optimise process conditions to enhance performance and yield.
- Troubleshoot common issues in catalytic reforming operations.
- Apply best practices in catalyst management and regeneration.
- Understand the environmental and safety aspects of catalytic reforming.
Target Audience
- Refinery engineers and operations professionals involved in catalytic reforming.
- Process engineers working on gasoline production or refining technologies.
- Operations managers responsible for overseeing catalytic reforming units.
- Technical staff and supervisors engaged in maintaining and optimising refining processes.
- Environmental and safety officers in refinery settings.
Daily Agenda
Day One: Introduction to Catalytic Reforming
- Overview of Catalytic Reforming: Understanding the role of catalytic reforming in refining and its contribution to high-octane gasoline production.
- Chemical Reactions in Catalytic Reforming: Key reactions (dehydrogenation, isomerisation, cyclisation) and the chemistry involved.
- Refinery Feedstocks for Catalytic Reforming: Types of feedstocks and their suitability for reforming processes.
- Reformate Properties: Properties of the reformate product and its uses in blending high-octane gasoline.
- Catalytic Reforming Units (CRU): Key equipment involved, including reactors, heat exchangers, and separators.
- Process Overview: Step-by-step guide to the catalytic reforming process flow.
Day Two: Catalysts and Reactor Design
- Catalyst Types: Overview of the various catalysts used in catalytic reforming, such as platinum and rhenium-based catalysts.
- Catalyst Deactivation and Regeneration: Understanding catalyst life, deactivation mechanisms (coking, poisoning), and regeneration methods.
- Reactor Design: Key considerations in the design of catalytic reforming reactors, including temperature, pressure, and flow dynamics.
- Temperature and Pressure Profiles: How process conditions impact the reaction rates and reformate yield.
- Catalyst Management: Best practices in catalyst loading, regeneration, and management.
- Hands-on Exercise: Catalyst sampling and analysis techniques.
Day Three: Process Control and Optimisation
- Catalytic Reforming Process Control: Key control parameters such as temperature, pressure, flow rates, and catalyst activity.
- Optimising Reforming Conditions: How to adjust process conditions to maximise yield and minimise coke formation.
- Energy Management in Catalytic Reforming: Strategies for optimising energy use in reforming operations, including heat recovery and integration.
- Troubleshooting Catalytic Reforming Issues: Common operational challenges (e.g., temperature fluctuations, pressure drops) and solutions.
- Monitoring and Control Systems: Overview of automated control systems used in catalytic reforming units.
- Case Study: Process optimisation in a real-world catalytic reforming unit.
Day Four: Environmental and Safety Considerations
- Environmental Impact of Catalytic Reforming: Emissions, waste products, and environmental regulations affecting catalytic reforming operations.
- Safety Concerns in Catalytic Reforming: Hazardous materials, high-temperature operations, and pressure risks.
- Catalyst Disposal and Waste Management: Managing spent catalysts and associated environmental concerns.
- Regulatory Compliance: Understanding global regulations governing catalytic reforming processes (e.g., emissions standards, safety protocols).
- Safety Systems: Safety systems in catalytic reforming units, including emergency shutdown and fire prevention systems.
- Group Discussion: Addressing safety and environmental challenges in catalytic reforming units.
Day Five: Troubleshooting and Performance Evaluation
- Troubleshooting Catalytic Reforming: Common operational problems (e.g., catalyst poisoning, poor reformate quality) and their solutions.
- Process Monitoring and Diagnostics: Techniques for monitoring reactor performance, catalyst activity, and product quality.
- Performance Evaluation: Methods for evaluating the efficiency of catalytic reforming operations, including yield, selectivity, and energy consumption.
- Case Study: Troubleshooting a catalytic reforming unit in a refinery setting.
- Future Trends in Catalytic Reforming: Innovations in catalytic reforming technologies and their potential impact on refinery operations.
- Final Assessment: Participants will apply their learning to solve a catalytic reforming case study.
Why Choose this Course?
This course provides a comprehensive overview of catalytic reforming, focusing on process optimisation, catalyst management, and troubleshooting techniques. Participants will gain valuable knowledge of the latest developments in catalytic reforming technology and best practices to improve efficiency, safety, and environmental compliance in refinery operations.
Learning Outcomes
Upon successful completion of the course, participants will:
- Understand the key principles and reactions involved in catalytic reforming.
- Be able to manage and optimise catalytic reforming processes to maximise product yield and quality.
- Have a clear understanding of catalyst management, including deactivation, regeneration, and disposal.
- Be able to troubleshoot common issues in catalytic reforming units and improve overall operational efficiency.
- Be proficient in monitoring and controlling catalytic reforming processes, ensuring optimal performance and compliance with safety and environmental standards.
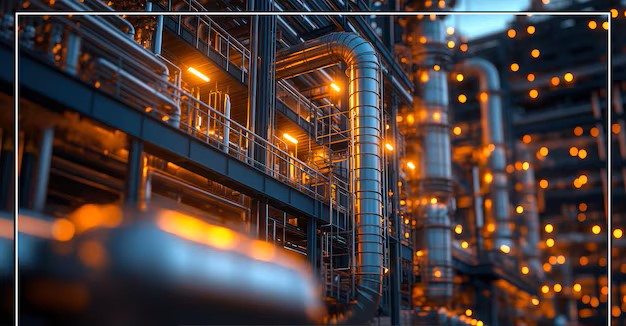