Process Equipment Failures: Prevention, Testing, Analysis, and Inspection | 14th – 18th July 2025
- Description
- Reviews
Course Overview
This 5-day course is designed to provide participants with an in-depth understanding of the causes and prevention of process equipment failures in industrial settings. Participants will explore various material testing methods, failure mechanisms, and diagnostic techniques used to assess and prevent failures in critical process equipment. The course covers practical tools for analyzing and interpreting failure data, as well as case studies on equipment failures, such as pressure vessels, heat exchangers, and pumps. Emphasis is placed on using advanced inspection, testing, and condition assessment methods to improve equipment reliability and extend asset life.
Course Objectives
By the end of this course, participants will be able to:
- Understand the fundamental causes of material and equipment failures.
- Apply materials testing methods, including tensile, impact, and hardness tests, to assess failure risk.
- Interpret failure data using analytical tools such as fractography, microscopy, and visual examination.
- Identify common damage mechanisms such as fatigue, wear, and corrosion.
- Utilize non-destructive testing (NDT) methods for effective inspection and condition assessment.
- Develop strategies for mitigating failure risks and extending the life of process equipment.
Target Audience
- Maintenance engineers and technicians.
- Plant operators and managers.
- Safety officers and engineers responsible for equipment reliability.
- Reliability engineers and corrosion specialists.
- Professionals involved in the inspection and assessment of process equipment.
Daily Agenda
Day One: Materials Testing and Failure
- Course objectives and overview.
- Materials testing: Tensile, impact, and hardness testing methods.
- Types of failures: Ductile vs. brittle fracture and the impact of temperature on material performance.
- Analytical tools for failure analysis: Visual examination, fractography, and microscopy.
- Industrial failure case studies: Real-world examples of failures and their causes.
Day Two: Damage and Interpretation of Failure I
- Stress concentration and its effect on material integrity.
- Introduction to fracture mechanics and its application in failure analysis.
- Understanding fatigue failure: Causes, symptoms, and prevention.
- High-temperature creep and its impact on equipment longevity.
- Thermal expansion and deflections: Analysis and mitigation strategies.
- Worked examples: Practical exercises in failure interpretation.
Day Three: Damage and Interpretation of Failure II
- Wear, galling, and fretting: Common damage mechanisms and their effects.
- Corrosion damage: Types, causes, and mitigation techniques.
- Vibration in equipment and piping: Causes and effects of vibrational damage.
- Vibration condition monitoring: Tools and techniques for detecting and managing vibration issues.
- Technical problem solving and decision-making approaches for failure prevention.
Day Four: Examples of Equipment Failure
- Pressure vessels: Common failure modes and strategies for life extension.
- Heat exchangers: Failure analysis and maintenance strategies.
- Pumps and compressors: Identifying failure points and implementing preventive measures.
- Mechanical seals and “O” ring failures: Causes, consequences, and solutions.
- Bearing failure: Detection, diagnosis, and maintenance practices.
- Pipe failures and repair techniques: Identifying common issues and selecting the right repair methods.
Day Five: Inspection, Testing, and Condition Assessment
- Non-destructive testing (NDT) methods: Introduction to various NDT techniques (e.g., ultrasonic testing, radiography, eddy current testing).
- Inspection of process equipment: Techniques for visual, mechanical, and NDT-based inspection.
- Examples of remaining life calculations for equipment.
- Overview of relevant inspection codes: API 570 and other industry standards.
- Course summary and wrap-up: Review of key concepts and best practices for preventing equipment failures.
Why Choose this Course?
This course offers a comprehensive approach to understanding and preventing process equipment failures, combining theory with practical application. Participants will gain hands-on experience with failure analysis techniques and learn how to apply them to real-world industrial settings. By mastering materials testing, damage interpretation, and inspection methods, participants will be equipped to enhance equipment reliability, reduce downtime, and improve safety within their facilities.
Learning Outcome
Upon completing this course, participants will:
- Understand and diagnose the causes of process equipment failures.
- Conduct materials testing and interpret failure data to assess risks.
- Identify damage mechanisms and apply appropriate mitigation techniques.
- Use NDT methods for the inspection and condition assessment of process equipment.
- Develop strategies to extend the life of critical equipment and prevent costly failures.
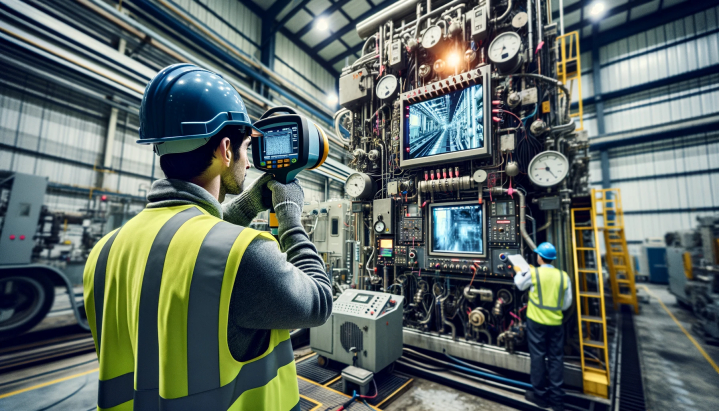