Refractory Systems Fundamentals Training 27th – 31st January 2025 (Weekdays)
- Description
- Reviews
Course Description
This course covers key concepts related to the design, installation, inspection, and testing of refractory systems. The courses will equip delegates with the necessary skills to assess the RISK of Refractory Failure and to examine Design Concepts. The courses cover the life of refractory linings from raw materials, purchase specifications, manufacturing, installation, heat-up and operation. Refractories are a critical part of the facility’s operation of most high temperature processes and play an essential role in many other industries. They are frequently a major cost item both in general maintenance and also in the unscheduled downtime of production units arising from premature refractory failure.
Who this course is for:
This training is will be beneficial for
Refractory Operations Crew
Maintenance Engineers
Metallurgists
Refractory Supervisors
Course Outline
1. Introduction to Refractories in Gas-to-Liquids (GTL) Projects
- Importance of refractory systems in GTL processes like those at Escravos.
- Overview of the GTL process: converting natural gas to liquid hydrocarbons via Fischer-Tropsch synthesis.
- High-temperature applications in GTL plants that rely on refractories, such as reformers and reactors.
2. API 936 Overview for GTL Projects
- Overview of API 936 and its relevance to the GTL industry.
- Specific guidelines from API 936 that apply to refractory selection, installation, and quality control in GTL facilities.
- Compliance with API 936 for refractory systems in high-temperature reactors, reformers, and heat exchangers.
3. Refractory Materials in Gas-to-Liquids Applications
- Selection of refractory materials suitable for GTL processes, including:
- Chrome-alumina and high-alumina refractories for reactors.
- Silica and ceramic materials for insulation and heat recovery systems.
- Specialized refractories resistant to chemical attacks from catalysts, synthesis gases, and hydrocarbons.
- Performance properties needed for GTL processes, including chemical stability, thermal conductivity, and resistance to thermal shock.
4. Detailed Description and analysis of the Key components of a refractory system
i. Refractory Lining
Types of refractory linings used in GTL plants:
o Dense refractory linings:
o Insulating refractory linings:
o Ceramic fiber linings:
ii. Anchors and Studs
i. Metallic or ceramic anchors
iii. Expansion Joints
· Flexible joints
iv. Castable Refractory
v. Refractory Bricks
vi. Mortar
· Refractory mortar
vii. Ceramic Fiber Modules
viii. Protective Coatings
ix. Insulating Backing Materials
x. Thermal Barriers
xi. Fiber-Reinforced Concrete
xii. Sealants
xiii. Heat Shields
xiv. Monolithic Linings
5. Detailed Description and analysis of the Instrumentation and Control system for a Refractory System of Gas-to-Liquids (EGTL) facility
i. Field Instruments
- Pressure Transmitters and Gauges
- Temperature Sensors
- Flow Meters:
- Level Transmitters
- Gas Analyzers
ii. Control Valves and Actuators
- Control Valves
- Globe valves, ball valves, and butterfly valves are typical in GTL applications, handling high pressures and temperatures.
- Actuators:
- Pneumatic actuators
- Electric actuators
- Hydraulic actuators
iii. Programmable Logic Controllers (PLCs)
iv. Distributed Control System (DCS)
- Describe how the DCS receives data from PLCs, field instruments, and analyzers to provide real-time process monitoring and control of critical units like:
- Fischer-Tropsch reactors, syngas reformers, gas purification units, and heat exchangers.
v. Human-Machine Interface (HMI)
vi. Safety Instrumented Systems (SIS)
- Emergency shutdown (ESD) systems
- Fire and Gas Detection Systems
vii. Supervisory Control and Data Acquisition (SCADA)
viii. Advanced Process Control (APC)
ix. Gas Chromatographs and Online Analyzers
x. Vibration Monitoring and Condition Monitoring Systems
· Vibration sensors
· Condition monitoring systems
xi. Power Management and Monitoring Systems
- Power distribution and control systems
- Power monitoring systems
- Alarm Management System
- Data Historian
- Networking and Communication Infrastructure
- Calibration and Testing Equipment
5. Description and analysis of typical operating parameters for a Refractory System of Gas-to-Liquids (EGTL) facility
i. Temperature
- Operating Temperature Range:
- Thermal Cycling
ii. Thermal Conductivity
- Low Thermal Conductivity
- Target Values
iii. Thermal Expansion
- Controlled Thermal Expansion
- Coefficient of Thermal Expansion (CTE
iv. Chemical Resistance
- Resistance to Syngas (Synthesis Gas)
- Fischer-Tropsch Catalyst Exposure .
- Alkali Resistance
v. Mechanical Strength
- Cold Crushing Strength (CCS)
- Hot Modulus of Rupture (HMOR)
- Abrasion Resistance
vi. Porosity
- Low Porosity
vii. Heat-up Rate and Curing Time
- Heat-up Rate
- Curing and Drying Time
viii. Gas Permeability
- Low Gas Permeability
ix. Thermal Shock Resistance
- High Thermal Shock Resistance
x. Erosion and Abrasion Resistance
- Erosion Resistance
xi. Refractoriness Under Load (RUL)
xii. Anchoring System Performance
xiii. Hydration Resistance (for Castable Refractories)
xiv. Refractory Lining Thickness
- Lining Thickness
xv. Insulation Efficiency
- Thermal Insulation Efficiency
6. Refractory Lining Design for GTL Equipment
- Designing refractory linings for high-temperature reactors, reformers, and syngas production units.
- Consideration of thermal stresses, mechanical loads, and chemical exposure in GTL operations.
- Expansion joints, anchor design, and refractory thickness calculations for GTL-specific equipment.
7. Installation Techniques for Refractories in GTL Plants
- API 936-compliant installation methods for castable, brick, and gunned refractories in GTL facilities.
- Challenges in installing refractories in complex geometries and high-stress zones of GTL reactors and heat exchangers.
- Best practices for ensuring the integrity and longevity of refractory linings in continuous high-temperature environments.
8. Curing and Drying of Refractories in GTL Facilities
- Procedures for the proper curing and drying of refractory linings in GTL units to avoid cracking and premature failure.
- API 936-recommended heat-up schedules, tailored to GTL processes.
- Preventing thermal shock and steam explosions during startup in gas processing environments.
9. Inspection and Testing of Refractories in GTL Projects
- API 936-compliant inspection techniques for refractory linings in critical GTL equipment.
- Non-destructive and destructive testing methods:
- Cold crushing strength (CCS) and hot modulus of rupture (MOR) for reactors and reformers.
- Chemical resistance tests for environments with high levels of synthesis gas (syngas) and catalysts.
- Conducting regular inspections during unit turnarounds and maintenance shutdowns.
10. Refractory Failure Mechanisms in GTL Plants
- Identifying and analyzing common refractory failure modes in GTL applications:
- Chemical corrosion from syngas and Fischer-Tropsch catalysts.
- Erosion and abrasion in high-velocity syngas and gas-reforming units.
- Thermal shock and spalling due to temperature fluctuations during startup and shutdown.
- Techniques for conducting root cause analysis and preventive maintenance based on failure analysis.
11. Refractory Maintenance and Repair in GTL Facilities
- Strategies for maintaining refractory integrity in continuous operation GTL units.
- Best practices for emergency repairs and patching of refractory linings in reactors and heat exchangers.
- Extending refractory life through proper operational practices, maintenance planning, and timely inspections.
12. Quality Assurance and Quality Control (QA/QC) in GTL Refractory Projects
- Implementing API 936 QA/QC protocols during refractory installation and maintenance in GTL projects.
- Documentation and reporting for regulatory and operational compliance.
- Ensuring material traceability and installation quality in GTL projects through checklists and on-site testing.
13. Case Studies: Refractory Applications in GTL Projects
- Examples from real GTL projects, focusing on refractory installations and performance in syngas reactors, reformers, and heat exchangers.
- Lessons learned from refractory failures and successes in similar gas-to-liquids facilities, including Escravos GTL.
14. API 936 Certification Preparation (Optional)
- Review of key topics for API 936 certification specific to GTL operations.
- Practice questions and strategies for individuals seeking API 936 certification in refractory quality control.
This course would be beneficial for engineers, maintenance personnel, and quality control staff involved in the refractory systems for the Escravos GTL project. The course focuses on ensuring long-term reliability and compliance with API 936 standards in high-temperature and chemically aggressive environments unique to the GTL industry.
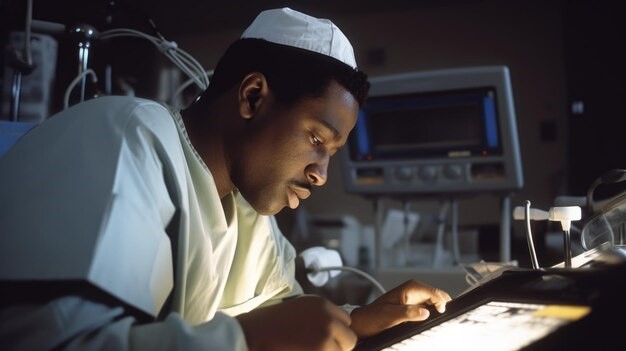